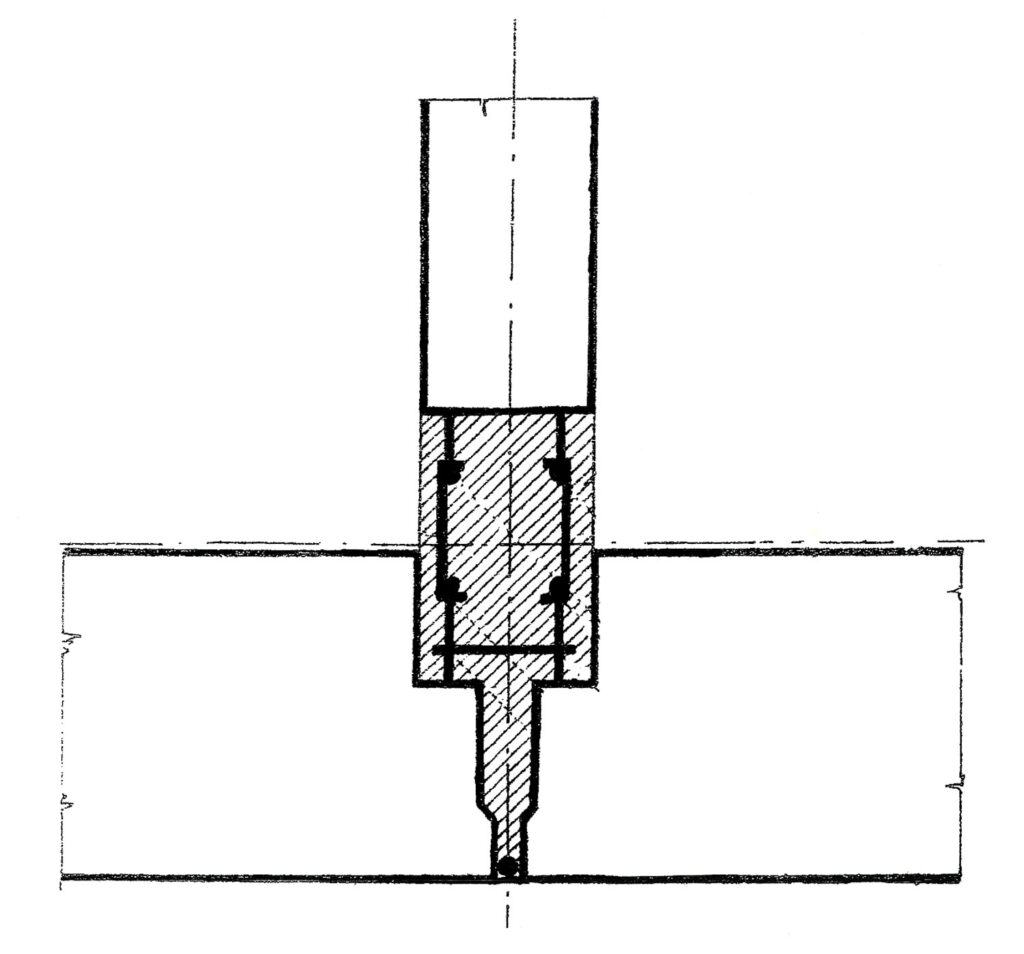
Mezi nejčastější příčiny závažných poruch panelových domů patří havarijní stav těsnění spár mezi jednotlivými panely. Následující text nabízí řešení za pomoci nových technologií renovace stávajícího těsnění, která jsou jak po funkční, tak i ekonomické stránce výhodnější než v současné době používané postupy, které jsou velmi pracné a nákladné.
Vzhledem k tomu, že již na počátku výroby panelů až po jejich montáž se vyskytovala řada technologických pochybení, vzniklo následně mnoho závad, které v častých případech nebyly odstraněny. Bohužel, současné hromadné zateplování „paneláků“ vyřešilo jen jeden problém (teplotní) a neodstranění dalších může způsobit selhání částí existujících konstrukcí.
Nevyhovující stav těsnění
Problematika těsnění spár obvodových plášťů montovaných staveb byla vždy složitým a rozsáhlým komplexem problémů, které v konečné fázi ovlivnily vlastní kvalitu a životnost stavebního díla a tím i pohodu bydlení.
Zamezení vnikání vlhkosti a vzduchu do stavebního díla bylo řešeno utěsněním svislých a vodorovných spár mezi plošnými prvky buď jednostupňově, nebo dvoustupňově. Lze předpokládat, že celková délka spár v ČR se pohybuje kolem 40 milionů metrů. Přehled vybraných konstrukčních systémů v ČR je uveden v tabulce 1.
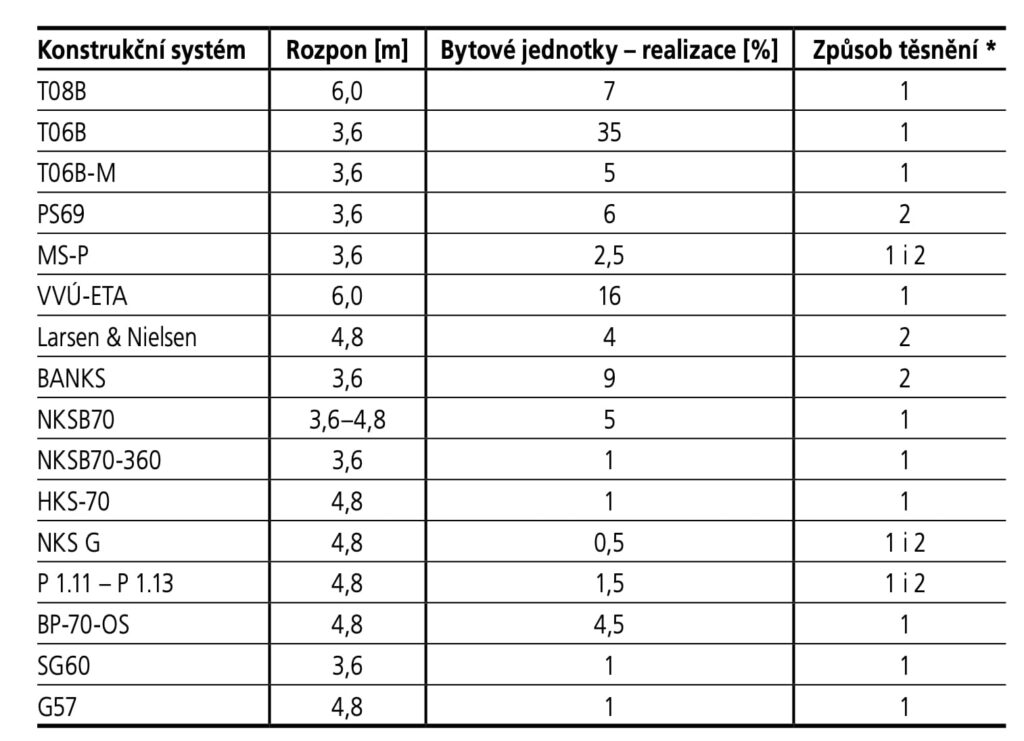
Tabulka 1: Přehled jednotlivých konstrukčních systémů (výběr)
Téměř 80 % všech spár je tedy těsněno tmely, případně jsou uzavřeny cementovou zálivkou (tvrdá spárová výplň) a zbytek spár je řešen použitím protidešťových zarážek a konstrukční úpravou prvků.
Převážná část konstrukčních systémů byla řešena s použitím vícevrstvých prvků (beton – polystyren – beton), a tudíž i pohyby vnější betonové desky jsou daleko větší než u jednovrstvých panelů.
I když tyto pohyby dosahují pouze 66 % vypočtené teoretické dilatace, byly a jsou pro řadu tmelů použitých do vnějších spár enormní.
Vzhledem k tomu, že toto utěsňování bylo zahájeno prakticky před 50 lety, je zřejmé, že v té době nebyly k dispozici odpovídající materiály a technologie. Řada dnešních závad je způsobena také vlivem nedodržování technologické kázně již v oblasti stavební výroby (překračování stanovených šířek spár, montáží prvků s poškozenými stykovými plochami, pevné spojení sousedních panelů vysprávkovou maltou, použití nesprávných podkladních profilů apod.).
Pro jednostupňový způsob utěsňování byly postupně používány spárové výplně uvedené v tabulce 2.
Možné tepelné pohyby stavebních dílců určené z rovnice
∆L = α·∆T·L,
kde ∆L – rozměrová změna délky prvku vlivem teploty [mm],
α – lineární koeficient délkové roztažnosti [°K-1],
∆T – teplotní rozdíl způsobující rozměrovou změnu [°K],
L – délka stavebního dílce [mm],
jsou do rozponu 4,8 m kolem 2 mm u vrstvených prvků. Při projektové šířce spáry 20 mm vznikala odpovídající poměrná deformace nad 10 %.
Např. u systému TO6B (obr. 1), který se z daných aplikací nejvíce realizoval, byly dříve používány pro těsnění spár tmely Barol a tmel olejový. Vzhledem k tomu, že jde o plastické typy tmelů, byly tyto materiály namáhány tahovou deformací v celém rozsahu pohybu spáry.
Tyto tmely nebyly schopny dlouhodobě přenášet takové deformace a docházelo k selhání utěsnění. Tomu napomáhalo i vlastní stárnutí tmelové hmoty, kdy její složení nezaručovalo větší životnost než 10 let.
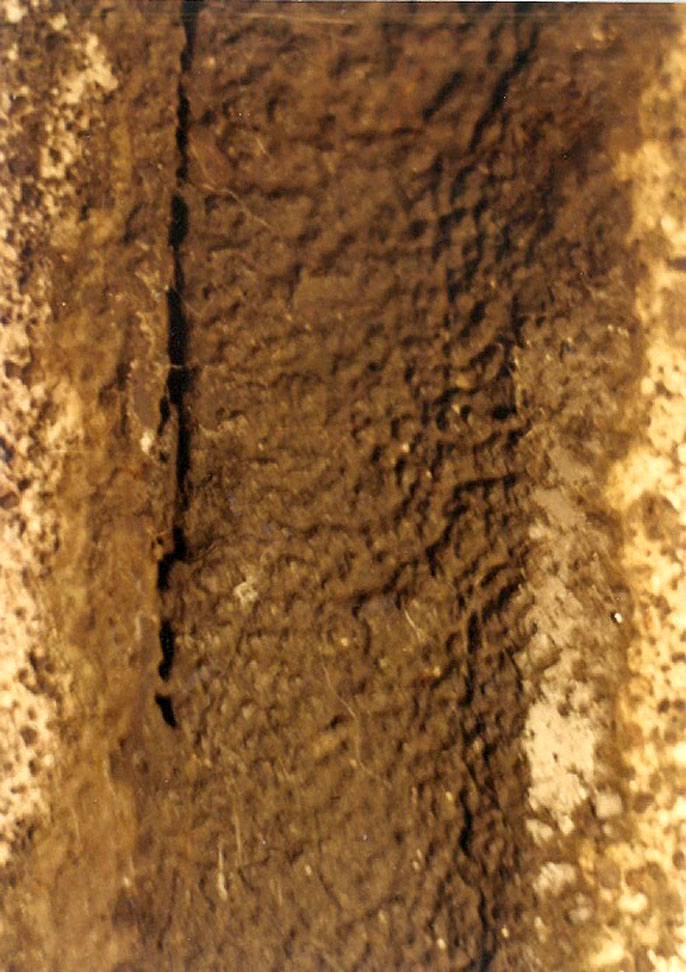
Toto se projevovalo v uživatelské sféře zatékáním srážkové vody a pronikáním vnějšího vzduchu do stavební konstrukce a následným vznikem plísní v interiéru na protilehlých místech svislých i vodorovných spár. Závažné poruchy se projevily i na ocelových výztužích sousedních panelů, kde jejich koroze způsobuje i v současné době značné zhoršení statiky budov. Například již v roce 2000 spadly obvodové panely na sídlištích v Brně, Ostravě a Praze. Nejstarší české panelové domy stojí ve Zlíně. První český čtyřpatrový „panelák“ tam byl postaven v roce 1953 s konstrukčním systémem G40.
Koncem 50. let byla zahájena v ČR výstavba panelových domů montovanou technologií a do začátku roku 2000 se předpokládalo, že existuje zhruba 1 200 000 bytových jednotek v různých konstrukčních systémech. Na přelomu 60. a 70. let minulého století, kdy v tehdejší ČSSR byl rozmach výstavby panelových staveb největší, řešily i kapitalistické země bytovou situaci pomocí tohoto systému výstavby. Největší rozvoj panelové výstavby byl v západní Evropě, a to především ve Francii. Dále se touto technologií zabývaly skandinávské země (Dánsko, Švédsko – „Miljonprogrammet“ 1965–74: 650 000 bytů). V 70. letech byla v evropských zemích bytová situace ustálena (díky industrializaci stavebnictví pomocí panelové výstavby) a postupně došlo k ukončení tohoto systému. Francie má v některých regionech a ve velkých městech dost velké sídlištní celky, které byly a jsou charakterizovány nízkou sociální stabilitou, spojenou většinou s vysokým podílem minoritních etnik z jiných zemí.
V zemích tzv. východního bloku se „Konstrukční stěnový systém z prefabrikovaných panelů“ (znění v ČSN – anglicky „Prefab“) uplatňoval v daleko širším rozsahu. Např. na Slovensku bylo v období let 1946–1989 realizováno 750 000 bytů. Na sídlišti Petržalka v Bratislavě to bylo cca 40 000 bytů. Dále větší procento těchto staveb se nachází ve městech Trnava, Košice (sídliště Luník IX), Prešov, Žilina (sídliště Solinky), Banská Bystrica, Nitra a Michalovce, kde v současné době lze nalézt větší množství rozestavěných paneláků s konstrukčním systémem např. Bauring-Camus.
V Polsku byl uplatňován konstrukční systém SP (dvanáctipatrové domy v Katovicích) a WPP – Waršava (sídliště Ursynów), s lidovým názvem „bloki“. Maďarsko („panelház“) odkoupilo dánskou licenci Larsen-Nielsen a na okraji Budapešti se rozprostírá velké sídliště s nezateplenou výstavbou.
V Rusku („chruščovky“) chtějí likvidovat pětipodlažní paneláky, ale výstavba nových bytů není vyřešena (Moskva, Petrohrad). V panelových bytech žije cca 80 % obyvatel zemí bývalého Sovětského svazu.
Bulharsko („panelki“) se ve městech Sofie, Ruse, Varna a Tolbuchin prezentuje na jejich okrajových plochách zanedbanými panelákovými sídlišti.
V Rumunsku („blocuri“) se v 70. a 80. letech minulého století v programu Nicolae Ceauşesca stavěly panelové domy v Bukurešti, Brašově a Albě Lulie. Paneláky lze nalézt i v Lotyšsku, Estonsku, Litvě, Mongolsku a řadě dalších zemí. Například v Německu („platenbau“) se rozjíždí prostorová prefabrikace. Bytové domy jsou sestavovány z hotových hranolovitých prvků vyrobených v betonárkách (dříve „Varie1“ – Swiss). Do zbylých a opravených klasických paneláků z plošných konstrukčních dílců se v současné době stěhují nájemníci (byty pronajímá spol. „Vonovia“, dříve DAI – Deutche Annington Immobilien). Než se podaří vystavět statisíce nových bytů, budou se určitě opravovat i staré paneláky v bývalém NDR, kterých se už hodně zdemolovalo. Průmyslové metody výstavby se uplatnily v roce 1957 ve městě Hoyswerda. Do roku 1990 byly realizovány 3 miliony bytů v panelových domech. K nejrozšířenějším typům patřily konstrukční systémy WBS 70, WHH GT 18, P2 a Q3A (Program Plattenbau-Neubaugebiet).
Vzhledem k tomu, že konstrukčních systémů bylo více a jednotlivé provádějící podniky měly své vlastní postupy při realizaci těsnění a povrchových fasádních úprav prvků, není možné provádět renovaci stávajícího těsnění jednotnou unifikovanou technologií. Podle situování těsnicí vrstvy v oblasti vnější zóny spáry může být renovace spár provedena novou těsnicí hmotou buď vyplněním, anebo překrytím.
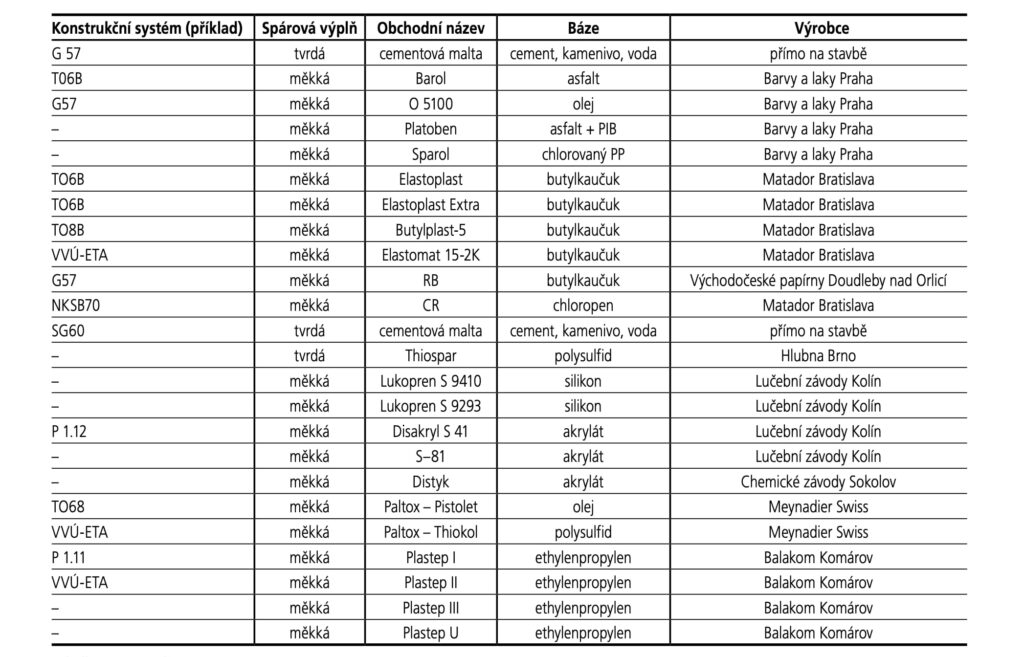
Skutečnosti, které časem vedly k porušení funkčnosti těsnění, jsou různé a lze je shrnout a charakterizovat v podstatě do čtyř základních oblastí:
● nesprávný návrh vlastního těsnění,
● nedodržování technologické kázně při výrobě, dopravě a montáži prvků,
● nedodržování technologických zásad a postupů při vlastních těsněních a vysprávkách panelů,
● kolísání kvality těsnicích materiálů.
V případě jednostupňového systému těsnění byla závadnost zapříčiněna překračováním stanovených šířek spár, případně překračováním jejich povolených tolerancí (vliv výrobních a montážních tolerancí) a nedostatečným vytvarováním, případně poškozením stykových ploch prvků v těsnicí oblasti (kaverny, ulámané hrany a rohy panelů apod.). V návaznosti na uváděné nedostatky výroby, dopravy a montáže, nekvalitně provedené vysprávky a úpravy spár (rozšíření/ zúžení spáry) se v daném případě jednalo o:
● provádění vysprávek za nevhodných povětrnostních podmínek (mráz, vysoké teploty apod.),
● pevné propojení navazujících panelů vysprávkovou hmotou, což mělo za následek vznik trhlin mezi vysprávkou a vlastním prvkem, neboť vysprávka nedokáže bez porušení soudržnosti s podkladem přenášet objemové změny prvků vznikající v důsledku kolísání teploty vnějšího prostředí. V daném případě se jednalo o velmi závažnou závadu, neboť srážková voda se dostala vlivem kapilárních sil za vlastní těsnění spáry, nemohla ze spáry vytéci na vnější fasádní líc, ve spáře se hromadila a způsobila jednak snížení tepelně-technických vlastností konstrukce a zatékala i do vlastního interiéru stavby,
● nesprávné použití podkladního profilu pod tmelovou vrstvu, což způsobilo enormní namáhání tmelové hmoty,
● nepoužití základního nátěru vedlo ke snížení přilnavosti – adheze tmelové vrstvy s podkladem,
● nedodržení předepsaných rozměrů tmelové vrstvy (šířka – tloušťka) a to mělo za následek její nepříznivé namáhání,
● tmelová hmota u spár I. nadzemního podlaží nebyla ochráněna a docházelo k jejímu odstraňování ze spár,
● nástřik fasádní povrchové úpravy přímo na tmel způsobil vznik trhlin v jeho hmotě. Vzhledem k tomu, že dvoustupňový systém těsnění nebyl z hlediska provádění tak technologicky náročný jako jednostupňový systém, byla u tohoto způsobu těsnění i nižší závadnost. Toto se projevovalo v oblasti spár především porušením požadovaného kritéria z hlediska neprůzvučnosti. Při nedodržování zásad těsnění dochází k průniku vnějšího prostředí do interiéru stavby, což mělo za následek porušení pohody bydlení a snížení tepelně-technických vlastností konstrukce obvodového pláště.
U dvoustupňového systému byla závadnost těsnění zapříčiněna překračováním maximální a minimální šířky spáry (vliv výrobních a montážních tolerancí) a nedostatečným vytvarováním, případně poškozením stykových ploch prvků v těsnicí oblasti (ulámané hrany a rohy, ozuby apod.).
Uváděné skutečnosti měly za následek, že se na obvodovém plášti objevovaly rozdílné šířky spár, které především při překročení rozměru minimální šířky 10 mm znamenaly, že do spár se nedá vložit těsnicí profil, který plní funkci proti- dešťové zarážky, a naopak při překročení rozměru maximální šířky spár 50 mm nebyl k dispozici profil, který by uváděné šířky zatěsnil.
Další závady se projevily v:
● nerovnoměrném podmaltování a jeho porušení v místě rektifikačních šroubů, popřípadě nedostatečná tloušťka podmaltování a nezapravení ložné spáry po provedeném osazení – montáž prvku,
● vkládání těsnicího profilu do spáry nedostatečných rozměrů, případně opomenutí jeho vložení, nedostatečném fixování profilu v požadované poloze a porušením jeho celistvosti, nevhodné volbě těsnicího profilu, který nesplňuje požadavky z hlediska neprůzvučnosti (provazce ze skelných vláken, asfaltem impregnované polyuretanové pásky apod.). Uváděné skutečnosti měly za následek zvýšení průniku vzduchu vnějšího prostředí do interiéru stavby, tzn. zhoršení uživatelských vlastností konstrukce.
Nevložením krytky do vodorovné spáry v místě křížení, případně:
● nedostatečným zakotvením a připojením krytky k podkladu,
● volbou nevhodného materiálu pro krytky (plech, lehká lepenka apod.),
● krytka nebyla dotažena až k fasádnímu líci a měla nedostatečný rozměr.
Následkem nevložení nebo špatného řešení krytky došlo k tomu, že srážková voda proudila po celé výšce stavby v poměrně velkém množství svislou spárou, až způsobila její průnik za protidešťovou zarážku do vlastního prostoru spáry.
Neplnění funkce druhého těsnicího stupně v oblasti svislé spáry při použití profilů z lehčené pryže bylo zapříčiněno:
● nedostatečným rozměrem profilu, který nebyl ve spáře kompresován,
● nedostatečným připevněním profilu ke stykovým plochám prvku, kdy na skládce, při dopravě a montáži docházelo k jeho oddělování od stykových ploch,
● nevhodně používanými materiály pro funkci druhého těsnicího stupně (provazce ze skelných vláken, polyuretanové pásky impregnované asfaltem apod.),
● v případě použití oplášťovaného tepelněizolačního dílce jeho nedosednutím do požadované polohy, případně jeho vynecháním – nevložením do stykového uzlu.
Následkem uvedených skutečností je, že se cementová malta zálivky stykového uzlu svislé spáry dostala (zatékala) do těsnicího prostoru spáry, tu vyplnila a v mnohých případech zatekla až do fasádního líce.
Vypadávání profilu plnícího funkci protidešťové zarážky spočívalo v:
● nedostatečném rozměru profilu, popřípadě jeho kompresi,
● jeho nenasunutí do správné polohy do vodicí drážky, případně jeho vložení do spáry v nevhodné poloze,
● použití nevhodných druhů profilů pro protidešťovou zarážku,
● tom, že profil nebyl po celé výšce panelu celistvý,
● porušení profilu nevhodným vkládáním do spáry (protahováním do spáry, používáním ostrých předmětů pro jeho zatláčení do spáry apod.).
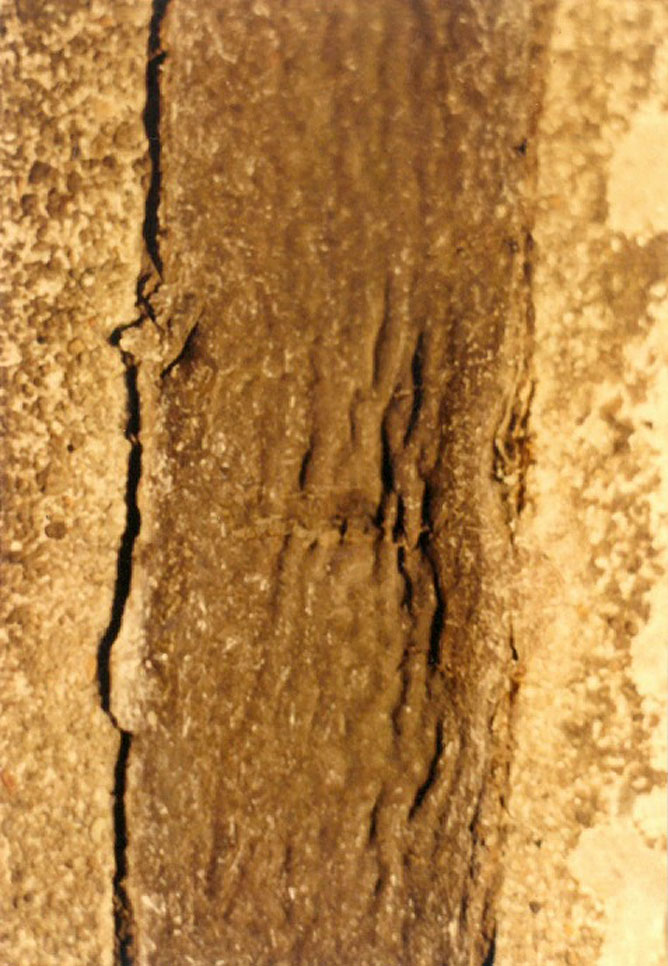
Uvedené nedostatky ovlivnily vlastní funkčnost těsnění svislých spár z hlediska vodotěsnosti a neprůzvučnosti.
Jak z uvedených skutečností vyplývá, projevilo se nedodržování technologických postupů při výrobě, dopravě a montáži ve snížení funkčnosti těsnění. V oblasti těsnění spár obvodových plášťů montovaných staveb se nepředpokládá během doby živostnosti těsnění v podstatě žádná údržba, a to jak u jednostupňové, tak i u dvoustupňové technologie.
Obdobná situace byla i v zahraničí. Bylo to dáno skutečností, že se jednalo o technologicky a ekonomicky náročnou záležitost. Vlastní závady vyplývající z dlouhodobé aplikace těsnění se objevovaly na stavbách postupně a jejich četnost byla ovlivňována různými faktory, mezi které patřila především životnost použitých těsnicích materiálů, způsob vlastního provedení těsnění, situování objektu v různých klimatických podmínkách a orientace stavby, stupeň mechanického namáhání apod.
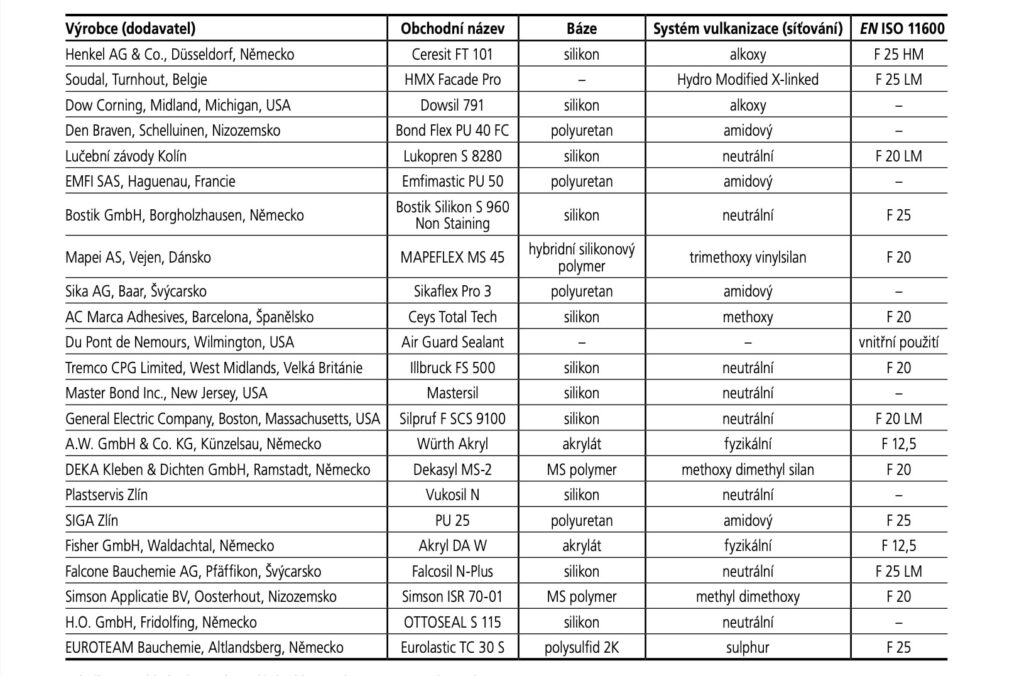
Volba vlastního způsobu renovace
Ta je prakticky dána a vychází ze stávajícího způsobu těsnění. V podstatě to značí, že v případě, že u stávajícího způsobu těsnění bylo použito jednostupňového systému těsnění, bude renovace prováděna opět jednostupňovým způsobem. U dvoustupňového těsnění spár je možné pro renovaci zvolit jedno- i dvoustupňový způsob.
Vlastní volba způsobu renovace je ovlivňována mimo uvedené celou řadou dalších faktorů, mezi které patří především způsob celkové renovace obvodového pláště, to znamená, zda bude prováděna pouze povrchová úprava fasádních ploch prvků, popřípadě tepelněizolační omítka, obklad, přizdívka, zateplení apod.
Jak z uvedených skutečností vyplývá, není možné provádět renovaci stávajících těsnění spár u všech montovaných stavebních soustav jednou unifikovanou technologií renovace, ale je nutné vycházet ze stávajícího stavu, tzn. druhu těsnění a rozsahu renovace celkové konstrukce obvodového pláště.
Renovace stávajícího těsnění spár, které již neplní svoji funkci, se provádí jedno- nebo dvoustupňovou technologií těsnění. Renovace těsnění spár jednostupňovým způsobem je z hlediska základního principu v podstatě stejná, jako byla u nové výstavby. Jedná se o zatěsnění spáry v jednom těsnicím stupni kombinací podkladního profilu a těsnicího tmele. Z hlediska provádění se od sebe odlišují různým situováním těsnicí vrstvy ve vnější těsnicí zóně spáry. Jedná se o renovaci spár, kdy těsnicí hmota spáry vyplňuje nebo překrývá.
Při stanovení/volbě těsnicího tmelu pro renovaci těsnění je nutné vycházet z dilatačního pohybu šířky spár, ke kterému dochází vlivem objemových změn prvků, vyvolaných kolísáním teploty vnějšího prostředí. Při volbě těsnicího materiálu se postupuje stejně jako dříve a pro renovaci použijeme tmel, jehož praktická tažnost Pt je větší než dilatační pohyb, ke kterému ve spárách dochází. Jedná se o způsob, kdy těsnicí hmota je situována do vlastní spáry a tuto v kombinaci s podkladním profilem vyplňuje. Podmiňujícím faktorem uváděného způsobu renovace je odstranění stávajících těsnicích materiálů ze spáry. Ve většině případů se jedná o odstranění těsnicích tmelů na bázi olejů, asfaltů, butylkaučuků apod., které vlivem dlouhodobého působení povětrnosti a mechanického namáhání již neplní v plné míře funkční požadavky z hlediska vodotěsnosti a neprůzvučnosti.
U spár, kde je stávající těsnění provedené cementovou nebo polymercementovou maltou a v oblasti těsnění spár se objevují trhliny, popřípadě vypadávání těsnicí výplňové malty, to znamená, že těsnění – výplň spáry – již neplní svou funkci, je nutno tyto materiály ze spár odstranit jako v případě těsnicích tmelů.
Při uvedeném způsobu renovace se odstraňují ze spár jak zestárnuté těsnicí tmely, tak i podkladní profily, a to v celém rozsahu spár. Obdobně se odstraní cementová malta, která se ze spár vyseká na hloubku 60–80 mm. Těsnicí materiály se ze spár odstraňují pomocí ručních nebo pneumatických sekáčů.
Další postup renovace spočívá v důkladném očištění stykových ploch prvků od stávajících těsnicích ploch, což je jedním z rozhodujících faktorů, na kterém závisí funkčnost nového těsnění – soudržnost tmelové plochy s podkladem.
Na ostění panelů po asfaltových tmelech, jako byl Barol nebo Plastoben (v receptuře použit např. asfalt AOSI 75/30), můžeme aplikovat tmely na polyuretanové bázi uvedené v tabulce 3. Jako penetrační nátěr lze použít roztok JOPLAST PU od firmy JoPoX, s. r. o.
Očištění stykových ploch lze provést roztokem ethylbenzenu v xylenu s poměrem obj. 20/80. Při těsnění vnějších spár tmely s olejovým podílem v receptuře (tmel olejový panelový 05 100, Elastoplast), kde byl použit lněný olej nebo minerální rafinovaný olej, docházelo k saponifikaci (zmýdelnění) na fázovém rozhraní ostění–tmel, kdy ionty hydroxidu vápenatého narušily vazby mezi uhlíkem a kyslíkem v triglyceridu (obr. 2 a 3). Stykové plochy lze čistit roztokem benzin/ aceton/buton-lol v poměru 6 : 2 : 2.
Pokud došlo při odstranění stávající cementové malty ze spár k poškození stykových ploch prvků, popřípadě se vyskytují nerovnosti, které by mohly narušit funkčnost těsnění, je třeba tyto vyspravit za použití polymercementové malty nebo tmelu.
Pro složení a provádění vlastní vysprávky platí stejné technologické zásady jako v případě výstavby. Po zaschnutí/zatvrdnutí vysprávky se do spáry vloží podkladní profil. Rozměr podkladního profilu by měl být takový, aby profil ve spáře držel v požadované poloze a fixoval tak tloušťku tmelové vrstvy. Po osazení profilu se stykové plochy prvků v těsnicí oblasti opatří základním nátěrem. Pro základní nátěr se používá příslušný penetrační roztok, který je pro jednotlivé tmely různý. Když základní nátěr zaschne, nanese se do spár pomocí spárovací pistole vrstva těsnicího tmele a provede se její dotlačení ke stykovým plochám prvků a zahlazení.
Jak z uváděných pracovních postupů renovace spár za použití jednostupňového systému, kdy těsnicí tmel spáru vyplňuje, vyplývá, jedná se o velmi pracný a nákladný způsob renovace, který je náročný na vlastní dodržování technologických zásad.
Nové technologie
Na základě uváděných skutečností jsou v současné době zaváděny pro renovaci stávajících těsnění spár nové technologie, které nevyžadují odstraňování stávajících těsnění ze spár. V daném případě se jedná o jednostupňové systémy těsnění, kde těsnicí materiál, ať již těsnicí tmel, nebo prefabrikované těsnicí pásky, vlastní spáru překrývá. Uváděné způsoby jsou jak po funkč- ní, tak i ekonomické stránce výhodnější.
Princip způsobu renovace spočívá v jednostupňovém zatěsnění spáry těsnicí hmotou, která spáru překrývá bez nutnosti odstranění stávajícího těsnicího materiálu ze spáry. Tento způsob renovace a těsnění je uplatňován i v zahraničí, kde se pro překrytí spáry používá elastický prefabrikovaný těsnicí pásek na bázi polysulfidu v kombinaci s dvousložkovým elastickým těsnicím tmelem stejné báze (obr. 4).
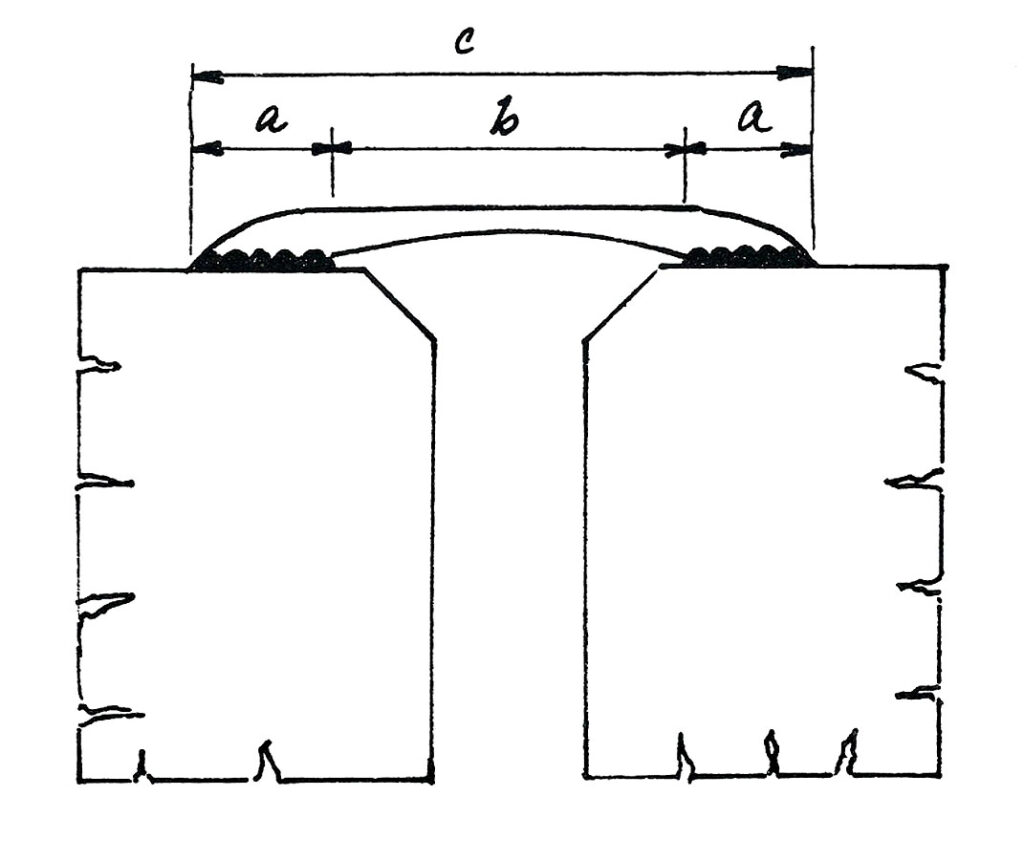
a – lepicí zóny; b – volná šířka pásku; c – celková šířka
Bohužel, v současné době jsou „paneláky“ zateplovány kontaktní izolační hmotou (polystyren, skelná vata, …), aniž jsou předem sanovány. Podle Aloise Palackého (odborný garant a autor bezkontaktních izolačních systémů FANA, s. r. o.) dochází pouze k zakrývání chátrají- cích stavebních konstrukcí. Kontaktní zateplení (např. ETICS – external thermal insulation composite system) nezajistí nutné provzdušnění daného souvrství.
Velmi závažné poruchy jsou ale v těchto zónách spár, v místech betonových výplní komor, ve kterých jsou vzájemně svařeny ocelové výztuže sousedních panelů. Jejich původní průměr 13 mm se vlivem průniku vlhkosti v některých místech snížil až na 4 mm a hrozí jejich úplné přerušení. Při použití ocelové výztuže, která nebyla plně pokryta cementovou směsí, se postupem času tvořily praskliny, které postupovaly radiálně od kovu do betonu vlivem koroze stavebního železa, jehož korozní produkty při snížení jeho průměru z 13 mm na 4 mm vytvářely objemové změny až 32 % (z 1 cm3 původního kovu vzniklo cca 10 cm3 rzi).
Pro vyhledávání a dokumentaci ocelové výztuže lze např. použít přístroj FS 10 Ferroscan.
Pro starší panelové domy byl proto navržen účinný, a přitom nenákladný způsob obnovení statiky, jehož podstata spočívá v tom, že se do komor, v nichž je propojena ocelová výztuž sousedících panelů, vyvrtají kanály, kterými se pod tlakem vpraví v tekutém stavu tuhnoucí organická tmelicí hmota, která v komoře vytvrdne.
Tmel v prvé řadě obklopí uvolněnou výztuž a izoluje ji před vodní párou. Vytvoří v komoře spolu s vydroleným betonem kompaktní náplň a pronikne rovněž do přilehlých spár mezi panely. Nanášení hmoty do uzlů se provádí speciálním zařízením (obr. 5).
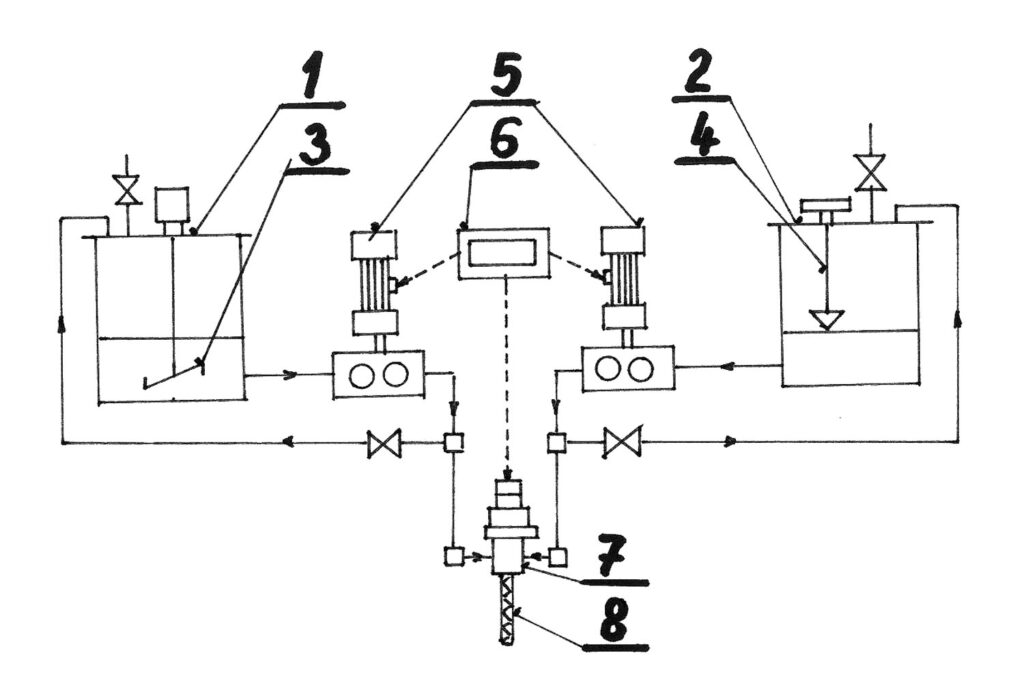
1, 2 – tlakové zásobníky složek A a B; 3 – míchadlo; 4 – hladinoměr; 5 – zubová nebo pístová čerpadla; 6 – řídicí jednotka; 7 – pistole NORDSON; 8 – statický mixér
Při stavbě panelového domu se obvodové panely spojovaly svařováním jejich výstupních ocelových prutů se stropními. Do tohoto styku se vkládala tepelná izolace (nejčastěji PS) a následovalo zalití cementovou maltou (χ = 17 MPa). Vnější spára měla být na závěr zatmelena. Tento postup nebyl ve většině případů dodržován a z toho důvodu docházelo ve velkém množství styků ke kondenzaci vodní páry v jeho vnitřním prostoru a následné korozi ocelového spojení. Obvodové panely tímto ztrácely dostatečné ukotvení, což vedlo a vede k jejich možnému vypadnutí z obvodových stěn.
Pokud panel vypadne nebo znatelně vybočí z obvodové linie domu, je nutno provést průzkum uzlů (komor) endoskopicky. Pro detekci vad v uzlu byl zvolen průmyslový endoskop, což je optická soustava, která je schopna přenášet světlo a obraz z uzavřených či jinak nepřístupných prostor směrem k pozorovateli. Toto je zprostředkováno tzv. inspekční trubicí, která se zavádí do daného místa.
Stereoskopické měření je poslední a zároveň nejpřesnější i nejrozšířenější metodou měření. Metoda je založena na principu stereoskopického (trojrozměrného) pozorování. CCD snímač je elektronicky rozdělen na dvě části. Na konci inspekční sondy je nasazen tzv. stereoskopický objektiv, který má k dispozici dvě čočky – levou a pravou, kdy každá z nich přenáší obraz na jednu polovinu CCD snímače. Rozdílem úhlů pozorovaného předmětu pak vzniká trojrozměrný obraz, kterým je pak mikroprocesor uvnitř videoskopu schopen trigonometrickou metodou vyhodnotit zkoumané prostory objektivem. Je možné použít např. přístroj Inspektor Pro/videoskop od Innovation Linkedin GmbH, Krefeld, Německo. Prozkoumají se uzly v celé budově a vyhodnotí se jejich technický stav. Může nastat situace, kdy:
● v uzlu (komoře) není zálivka (beton) vůbec. Do uzlu je potřeba vpravit aplikační hmotu v množství 2,0 l o tmelové viskozitě kolem 50 Pa · s,
● v uzlu je betonová drť, injektujeme tedy hmotu s viskozitou 5000 až 10 000 mPa · s,
● v betonu jsou jen trhliny – aplikuje se hmota o viskozitě kolem 1000 mPa · s,
● komora je plná neporušeného betonu.
Jako injektážní materiály se používají polymerně tvrdnoucí nebo hydraulicky tvrdnoucí injektážní hmoty. Výběr injektážního materiálu se řídí v zásadě jeho mechanickými vlastnostmi v teplotním rozsahu použití. Zatímco minerální injektážní hmoty se základním pojivem cementem se chovají podobně jako beton, polymerní materiály mají mechanické chování závislé na teplotě (duromery, elastomery). Schopnosti přetvoření jsou díky teplotnímu rozsahu zesklovatění značně odlišné. Z praktického hlediska je pro injektáž velmi důležitá směsná viskozita výplňového materiálu. Podstatně určuje hranice jeho použití. S polymerními injektážními materiály (reakčními pryskyřicemi) lze provádět injektáž trhlin od šířky 0,1 mm. Vzhledem k dobré kapilární vzlínavosti jsou umělé pryskyřice schopny proniknout až do kořene trhliny a srovnatelných rozvětvení. Materiální suspenze jsou omezeny na injektáž širších trhlin v závislosti na struktuře částic pojiva. Navíc nemohou být trhliny naplněny minerálními suspenzemi plně až k jejich kořenům. Proto nelze tímto způsobem zajistit utěsnění trhlin.
Významným pojivem pro polymer vysprávkové hmoty jsou epoxidové pryskyřice. Jejich kladem je výborná adheze k široké škále anorganických plniv, malé smrštění při vytvrzování, dobrá objemová stálost, velká mechanická pevnost při statickém a dynamickém dlouhodobém namáhání, dobrá povrchová tvrdost, výborné dielektrické vlastnosti, dobrá odolnost vůči chemikáliím, vodě, povětrnosti, malé stárnutí apod.
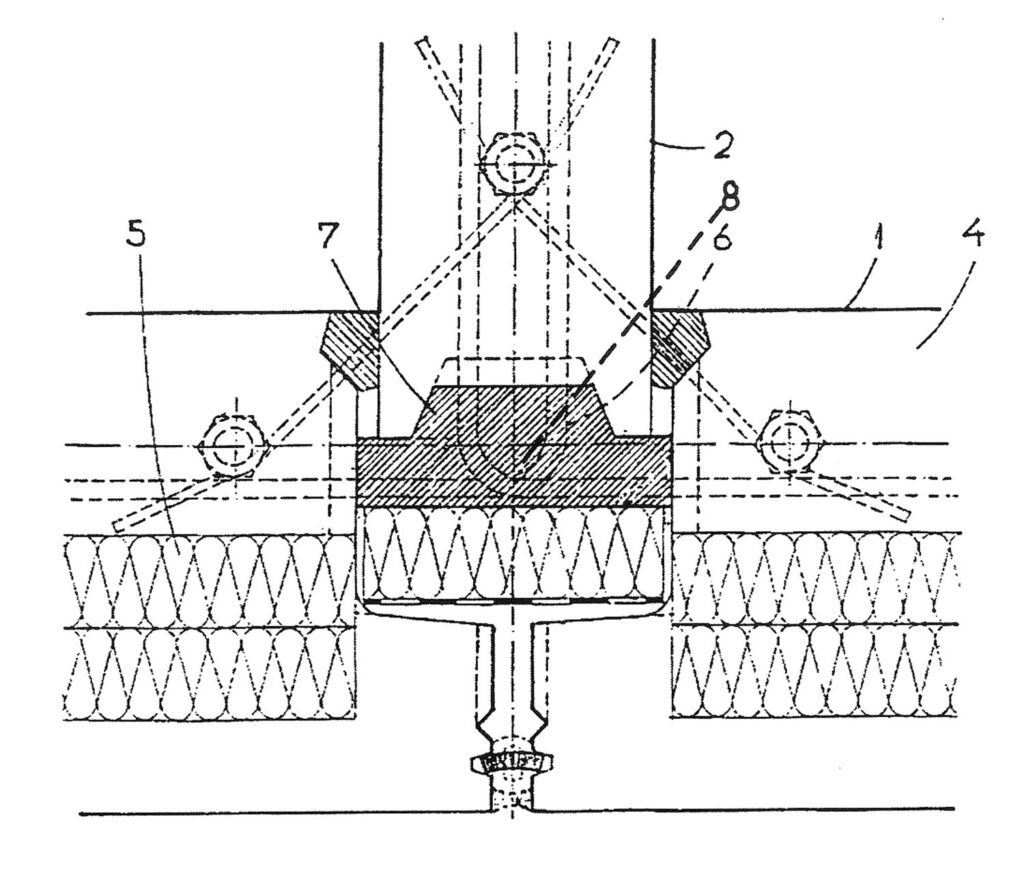
1 – obvodový panel; 2 – příčná nosná stěna; 4 – betonová část plášťového
panelu; 5 – tepelná izolace; 6 – ocelová výztuž; 7 – komora (uzel); 8 – navržený vývrt
Sanace obvodových stěn panelových budov způsobem injektáže zpevňujících polymerních hmot do daných uzlů (komor) styků panelů je nová technologie, která rychle a systémově tento problém řeší. Poruchy, které se v této oblasti vyskytují, jsou trhliny a kaverny v zalévací betonové směsi a koroze ocelové výztuže (prutů z oceli 11373, 10425, 10002 nebo 10370). Pro realizaci tohoto záměru je nutno posoudit stav konstrukce daného uzlu, a to endoskopicky, objevit trhliny a kaverny.
Z obr. 6 je zřejmý styk plášťových panelů 1 s panelem 2 příčné nosné stěny a z obr. 7 jejich styk se stropním panelem 3. Jako 4 je označena nosná betonová část plášťového panelu 1, jako 5 tepelná izolace, jako 6 vyčnívající ocelová výztuž určená ke svaření s výztuží 6 sousedního panelu. Konečně vztahovou značkou 7 jsou označeny komory – zvýrazněné šrafováním, které byly, v lepším případě, po smontování panelů 1, 2, 3 vyplněny betonem. Na obrázku jsou vyznačeny i vrty do uzlů čárkovaně. Do vyvrtaného otvoru v obvodové vnitřní stěně panelu se zasune pod úhlem cca 45° pakr (např. OPK 10/100 – M – 5), jehož průměr a délka se volí na základě provedené diagnostiky. Spojení se statickým směšovačem se provede pomocí tlakové hadice a pakrové spojky.
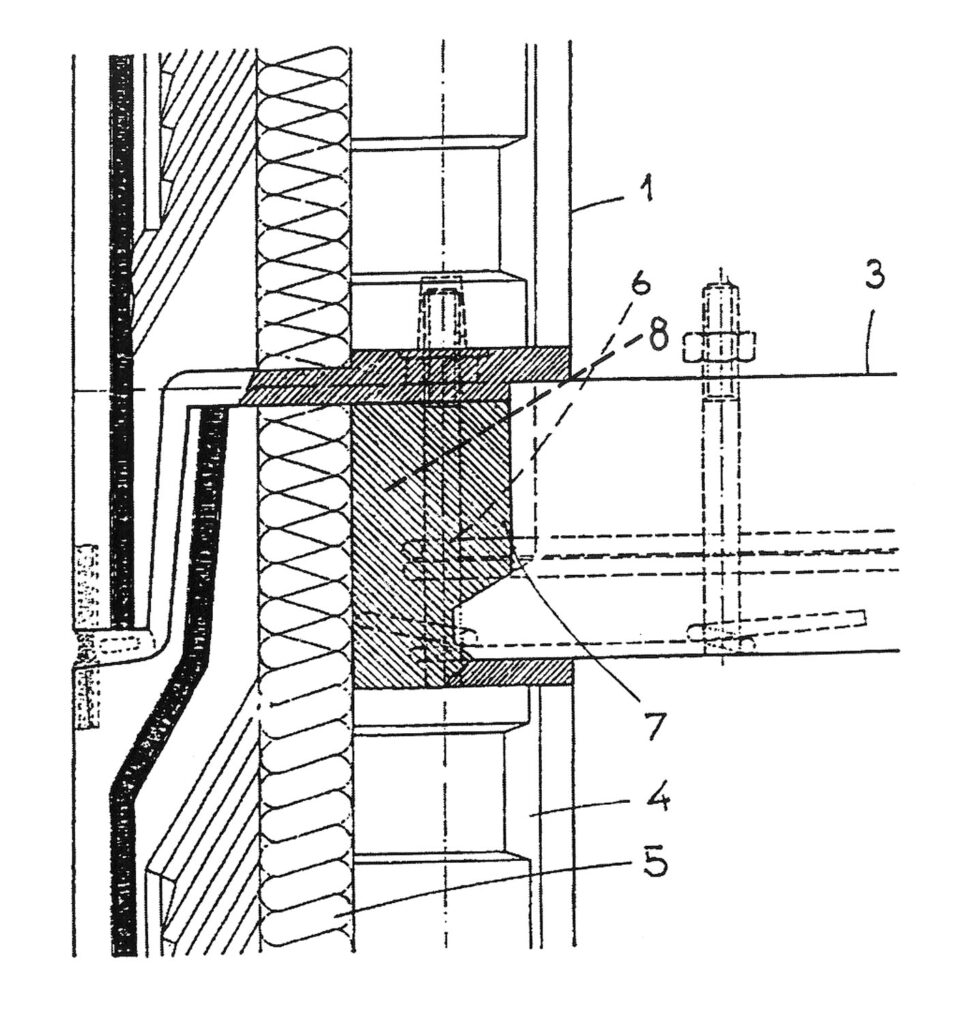
Obr. 7: Vodorovná spára konstrukčního systému
3 – stropní panel (ostatní pozice viz obr. 6)
Na pakru je upevněna hadice a ta je připevněna ke statickému směšovači injektážní pistole. Postupně dochází k vyplňování pakru, jeho otvoru a prostoru s trhlinami nebo drtí injektážním materiálem. Pístové čerpadlo je nastaveno na nejnižší tlak. Pomalá injektáž za nízkého tlaku je účinnější než rychlá a vysokotlaká (do 80 barů). Vysoký tlak během injektáže může poškodit strukturu konstrukce uzlu a navazujícího prostoru střední zóny spáry, i případného zateplení. Dopravování materiálů A a B směsí je prováděno z tlakových zásobníků různých velikostí. Směšovací poměry lze nastavit spojením pneumatického pohonu s oběma čerpadly. Směšovač sestává ze dvou výstupních ventilů a statického mixéru s elektrickým nebo pneumatickým ovládáním. Sestava je navržena tak, že při přerušení toku (uzavření ventilů) vznikne zpětný sací efekt, který zamezí dalšímu výtoku, např. pryskyřice. Celý směšovací systém umožňuje mísení A i B složek s různými viskozitami i mísicím poměrem.
Statický mixér (směšovač)
Jde o pevné, nepohyblivé, vhodně tvarované vestavby instalované ve štěrbině kruhového nebo čtvercového průřezu, pro kontinuální míchání např. pryskyřičných roztoků.
Pro správnou volbu mixéru je nutno znát objemový průtok látek a jejich příslušné fyzikální vlastnosti (hustotu, viskozitu, rheologické chování apod.). Vychází se z rychlosti proudění, zvoleného průměru hubice, počtu a uspořádání vnitřních elementů, stavební délky mixéru a jeho tlakové ztráty. Výběr čerpadel a dávkovacího zařízení pak určuje požadovanou aplikační funkci.
Parametry se stanovují experimentálně, poněvadž teoretické řešení návrhu statického mixéru je vzhledem ke složitému třírozměrnému proudění a nespojitosti obtékaných ploch velmi komplikované.
Při přípravě roztoku dopravovaného do opravdového místa je nutno namíchat směsi A i B tak, aby se jejich hustoty lišily minimálně. Při směšování kapalin s rozdílnými hustotami může totiž ve vodorovné trubici s vestavbou dojít k nežádoucímu rozvrstvení roztoků a k homogenizaci dochází minimálně.
Vzhledem k tomu, že statické mixéry mají poměrně malou axiální disperzi, je nutno, aby látky vstupovaly do elementů mixéru vedle sebe a docházelo i k jejich radiálnímu míchání. Pístová čerpadla proto musí pracovat s velkou frekvencí otáčení a rovnoměrné dávkování se projeví v dobré kvalitě homogenizace.
Problém nastává při použití vláknitých plniv ve směsích A i B. Při větších rozměrech vláken dochází k jejich hromadění na náběžných hranách elementů mixéru a postupnému blokování mísení.
Plocha článku se stáčí o 180° (vždy na opačnou stranu). Čelní plocha dalšího článku je kolmá na plochu předchozí a pootočená o 90°. Dokonalé promíchání složek u různých bází – viz tabulka.
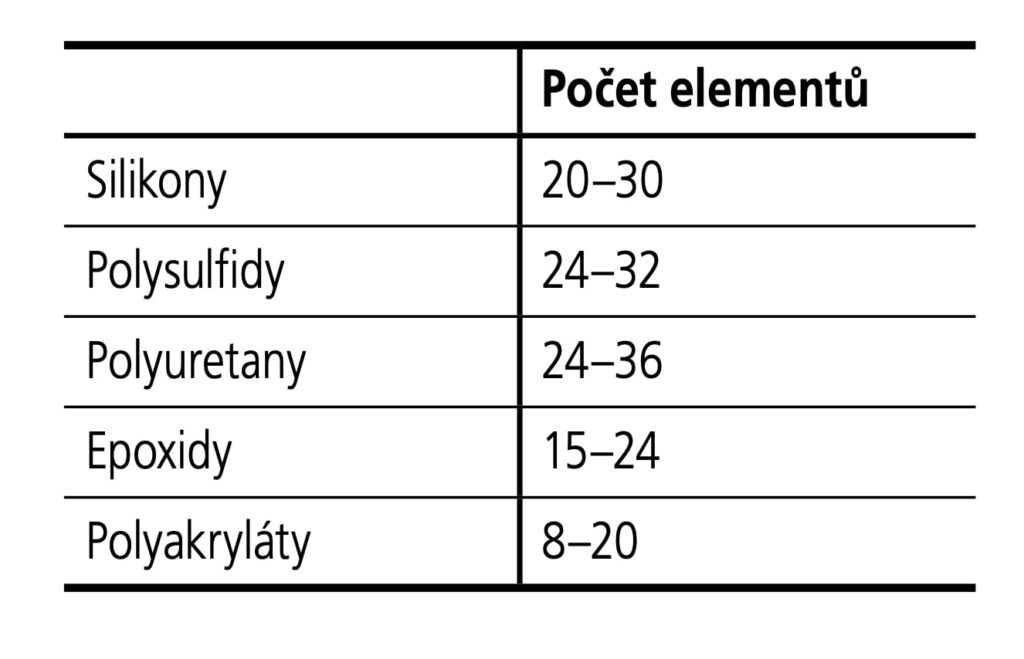
Rovné čelní plochy těchto článků zároveň omezují i průtočný průřez v místech jejich křížení. U prvku s vnitřním průměrem 10 mm a šířkou hrany segmentu 2 mm by se průtočná plocha zmenšila o 15 % a došlo by ke značnému poklesu tlaku kapaliny (směsi). Z toho důvodu je nutno dávat přednost statickým mixérům (obr. 8), kde každý článek má na jednom konci tzv. nožovou hranu vzniklou sražením dvou jeho protilehlých hlavních ploch.
Nepohyblivá součást mixéru tedy spočívá v sérii souosých přepážkových prvků, nejlépe se segmenty střídavě s pravým a levým šroubovým zakřivením, přičemž nožové hrany sousedních přepážek jsou vzájemně kolmé. Střídavý pohyb po šroubovici vnucený tekutině s opakovaným oddělováním a spojováním různých částí s různou rychlostí na dalších článcích, působí velmi intenzivní míchání. Průchod kapaliny kolem prvku se dělí mezi symetrické polokruhové průchody. U konce prvku se průchod mění na asymetrický s posunem kolem středového jádra s převracením. Navíc nožová hlava náběhové a odtokové přepážky zvyšuje průřezovou průtokovou plochu při přechodu mezi sousedními přepážkami a tím i rychlostní gradient míchacího toku.
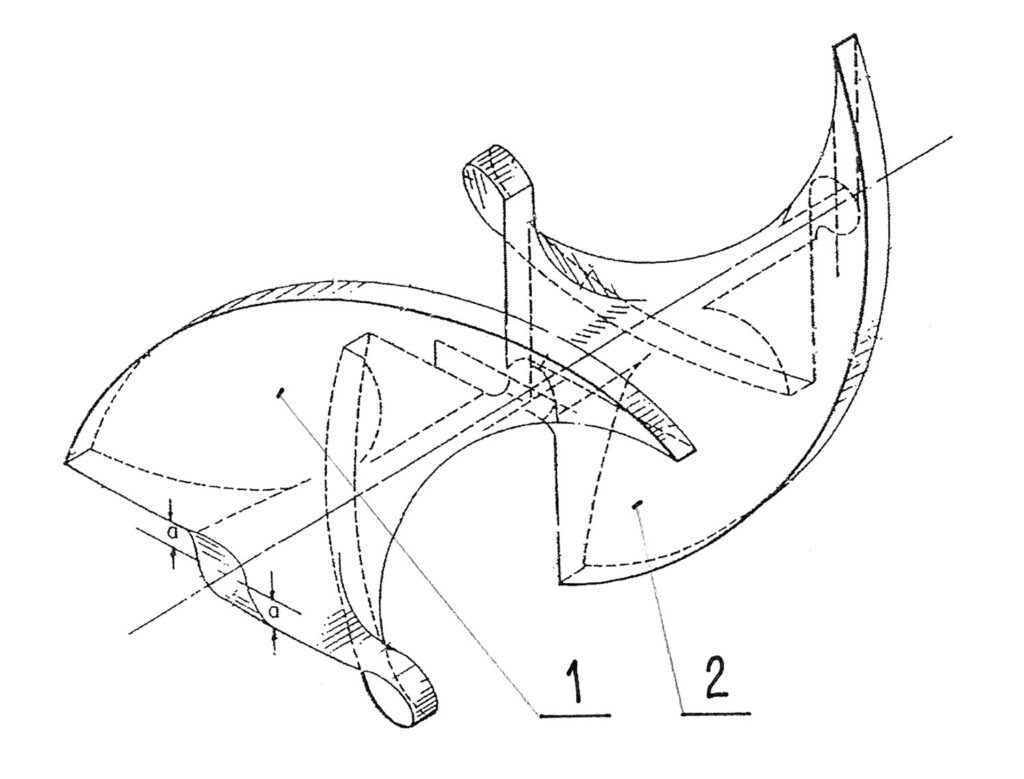
1 – přepážka s pravým zakřivením; 2 – přepážka s levým zakřivením
Výhodou dvousložkových chemicky reagujících směsí je jejich rychlost síťování po nanesení do trhlin a spár. Pohybuje se od cca 5 minut do 60 minut a hmota již po této době výrazně nemění své fyzikálně-mechanické vlastnosti.
Cílem byl vývoj co nejúčinnějšího statického směšovače s minimální tlakovou ztrátou. Mísicí elementy jsou vzájemně natočeny o 90°. Homogenizace a dispergace probíhá v laminárním proudění a umožňuje i dávkování nízkoviskózní tekutiny do hlavního, vysoce viskózního proudu. Směšovač umožňuje použití pro široký rozsah viskozit, při minimální degradaci produktu, díky krátkému držení média uvnitř trubice. Velký rozptyl střižných sil zároveň umožňuje i dispergaci těžko mísitelných tekutin.
Předností směšovacího zařízení se statickým mixérem je možnost směšovat A a B komponenty s velmi odlišnými viskozitami a s velmi extrémním směšovacím poměrem. Ve směšovacím bloku je tlak materiálu rovnoměrně rozložen a je zaručeno současné dávkování komponent. Pro kontrolu množství materiálu v tlakovém zásobníku je možno tyto nádoby vybavit hladinoměry.
Dokonalé promíchání obou složek A i B závisí na konstrukci použitého statického mixéru. Musí být navržen tak, aby obsahoval přepážky (závity) rozdělující a opět směšující kapalinu i invertované přepážky odvádějící kapalinu od vnějších stěn. Spirálové přepážky prodlužují oblast směšování tak, aby na výstupu mixéru byla pouze koncentrace, která odpovídá koncentraci smísených kapalin v celém průřezu. Mixér má zároveň umožnit vstup obou složek do mísící trubice pod stejným úhlem.
Na základě inženýrského přístupu k toku nenewtonských kapalin z hlediska rheodynamické koncepce (quasi/visko/metrické proudění) je možno na základě laboratorních dat uspokojivě předpovědět chování reálných směsí v reálných podmínkách.
Ponorná rotační viskometrie (např. přístroj Rheotest) dovede posoudit z globálního průběhu rotačního toku vlivy elastických efektů reprezen- tovaných normálovými pnutími a jejich přenos do proudění v kapiláře.
Při vstupu hmoty do volného prostoru (např. konstrukční uzel nevyplněný betonem) je nutno její míru thixotropie zajistit nestékáním v komoře. Naopak v systému prasklin (trhlin) betonu (např. v zkoumaném uzlu) je nutná vzlínavost roztoku a odpovídající index toku této skutečnosti.
Praktická zkouška s upravenou ruční pistolí (poměr 3 : 1) ukázala na reálnost uvažované technologie. Výsledné receptury směsí (A a B) pak vzejdou z dalších modelových zkoušek.
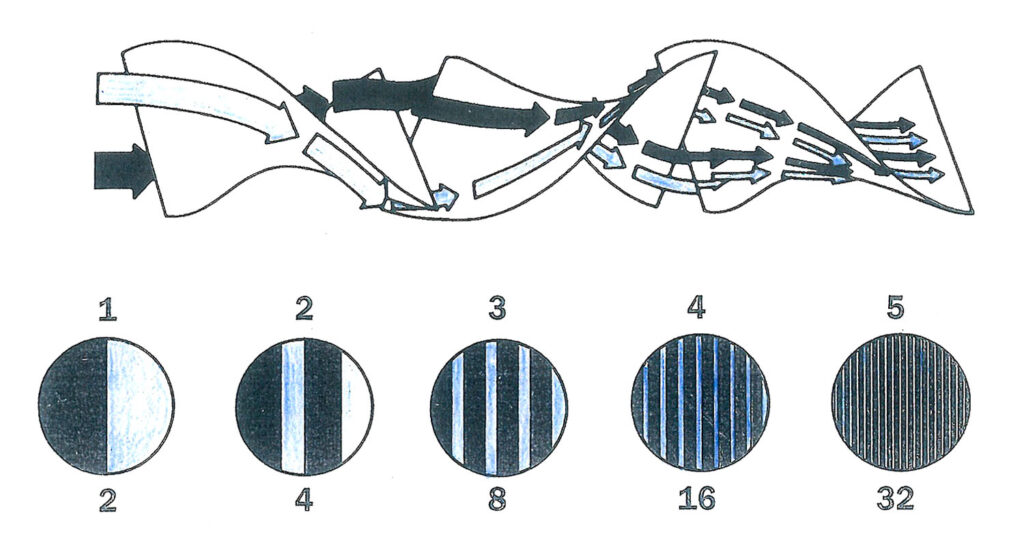
Funkce segmentů
Podle obr. 9 má přepážka (segment) dvě plochy ležící obvodově protilehle, obecně s pravým šroubovitým zakřivením kolem středové osy. Jsou tvarované tak, aby těsně doléhaly k vnitřní stěně tělesa tvořícího válcový prostor. Levá přepážka má podobně dvě protilehle ležící šroubovitě zakřivené plochy.
Za provozu jsou dvě tekutiny vedeny do zařízení na protilehlých hlavních zakřivených plochách první přepážky. To schematicky znázorňuje obr. 9:
Střídavý pohyb po šroubovici vnucený tekutině s opakovaným oddělováním a spojováním různých částí s různými rychlostmi na dalších přepážkách způsobí intenzívní míchání. Průchod kapaliny kolem prvku se dělí mezi symetrické polokruhové průchody. U konce prvku se průchod mění na asymetrický s posuvem kolem středového jádra a jeho převracením.
Navíc nožová hrana náběhové a odtokové přepážky zvyšuje průřezovou průtočnou plochu při přechodu mezi sousedními přepážkami a tím zvyšuje i rychlostní gradient míchacího toku. Rozdělení vrstev na jednotlivých článcích lze popsat rovnicí:
N = 2i,
kde N – počet vrstev,
i – počet článků.
Při počtu článků i = 20 je počet vrstev roven 1 048 580.
Závěr
U dosud nezateplených objektů je nutno opravit spáry u obvodových panelů. Kondenzace vodní páry v jejich vnitřním prostoru způsobila následnou korozi ocelových spojů.
U již zateplených budov je po endoskopickém průzkumu uzlů možno provést jejich zpevnění zevnitř, injektážní hmotou dle patentu ČR č. 307621.
ADOLF MUSIL
Ing. Adolf Musil (* 1945)
po maturitě na Střední průmyslové škole strojírenské ve Zlíně vystudoval na VUT Brno, Fakultě technologické obor syntetických polymerů. V roce 1970 nastoupil do VÚPS Praha na pozici odborného asistenta vývoje polymerních a elastomerních těsnicích materiálů. Během působení v této společnosti obdržel řadu patentů. V roce 1982 jako člen JZD Slušovice řídil výstavbu biotechnologických laboratoří a provozů a později se stal zástupcem ředitele. Je autorem knihy „Spárové těsnicí tmely ve stavebnictví“, kterou v r. 1985 vydalo SNTL Praha. Od r. 1991 samostatně podniká jako OSVČ ve výzkumu a vývoji lepicích a těsnicích směsí včetně betonových s využitím bioremediace.
Publikováno v časopise Materiály pro stavbu 5/2024
Literatura
Tomis, F.: Základy gumárenské a plastikářské technologie. Učební texty UTB Zlín.
Vynález č. 294888, Musil, A., van der Veen, A.: Způsob obnovení statiky panelových domů. ÚPV, Praha 2005.
Vynález č. 307621, Musil, A.: Dvousložkový organický tmel pro stavebnictví. ÚPV, Praha 2019.
Guzman, R. Z. & col.: Rheologica Acta 58, No 5, 2018.
Palacký, A.: Zateplování zchátralých domů. Ateliér č. 2/2010, r. 14, s. 18–19.
TZFV 20336: Výzkum a vývoj nové technologie sanace obvodových uzlů konstrukce panelových domů. Projekt MPO 2020.
Crow, J.: Epoxy Resin. W. W. Norton & Co., 2023, 192 s.
Stanciu, I.: Reologia dei materiali tessili. Edizioni Sapienza, 2022, 76 s.
Protokol o zkoušce: Dvousložkový epoxidový tmel – únosnost. KAMi, s. r. o., Otrokovice, 2021.
Leemann, A. & col.: Alcali Silica Reaction in Concrete. Cement and Concrete Research, sv. 176, USA 2024.
Huang, J. & col.: The industrial SO2 – induced corrosion. Cement and Concrete Composites, sv. 150, Kanada 2024.
Musil, A., Mitáček, P.: Přeplátované spoje. Materiály pro stavbu, ročník XXVIII, č. 4, s. 48- 50, 2022.
Musil, A., Mitáček, P.: Spoje na tupo. Materiály pro stavbu, ročník XXIX, č. 4, s. 57–59, 2023. Musil, A., Mitáček, P.: Tmely do dilatačních spár v betonových dílcích. Materiály pro stavbu, ročník XXX, č. 2, s. 28-33, 2024.
Nejnovější komentáře