Ultravysokohodnotný beton (UHPC – ultra high performance concrete) je jednou z největších výzev moderní technologie betonu po celém světě. UHPC je beton s pevností výrazně nad normově danými třídami, s dlouhou trvanlivostí a odolností pro nejnáročnější podmínky. Tento článek shrnuje dosavadní zkušenosti s vývojem, výrobou, dopravou a ukládkou tohoto betonu u společnosti TBG METROSTAV.
Co je UHPC
Jak už bylo zmíněno výše, UHPC označuje betony s extrémně vysokou pevností a trvanlivostí. Není ovšem žádná celosvětově uznávaná norma nebo předpis, který by stanovoval, jakých parametrů musí beton dosáhnout, aby se dal do kategorie UHPC zahrnout. Nejčastěji, zejména v sousedním Německu, je zmiňována hranice pevnosti v tlaku na válcích 150 MPa. Je tedy zřejmé, že pevnosti UHPC jsou výrazně nad stanovenými pevnostními třídami v normě ČSN EN 206-1/Z3. V této normě je nejvyšší pevnostní třídou třída C100/115, tzn. válcová pevnost v tlaku 100 MPa. Model Code FIB 2010 ještě připouští pevnostní třídu C120/140, tzn. válcovou pevnost 120 MPa. První hlavní výhodou UHPC je tedy velmi vysoká pevnost, která umožňuje zmenšit průřezy konstrukcí a snížit tak vlastní hmotnost konstrukce.
Druhou hlavní, a možná ještě důležitější, výhodou je výrazně zvýšená trvanlivost konstrukce z UHPC.
V literatuře se uvádí životnosti více než 200 let a zejména tato zvýšená životnost ospravedlňuje zvýšené náklady na beton. Tento beton se nejčastěji navrhuje do prostředí s vysokým namáháním chloridy, mrazovými cykly nebo chemicky agresivními látkami.
Složení UHPC
Známé receptury UHPC se vyznačují velmi vysokými dávkami pojiva a mikrosiliky, extrémně nízkým vodním součinitelem a vysokou hutností uloženého betonu. Složená křivka zrnitosti směsi musí být optimalizována od nejjemnějších částic (mikrosilika) až po hrubé kamenivo. Hrubé kamenivo může mít zrnitost až 16 mm, ovšem běžně má maximální zrno průměr do 8 mm. Celkově je směs velmi jemnozrnná.
Základem pro dosažení požadovaných pevností a odolností je co nejvyšší hutnost uloženého betonu. Vodní součinitel UHPC se běžně pohybuje okolo hodnoty 0,2. Je tedy vidět, že ve směsi není dostatek vody na úplnou hydrataci pojiva.
Pojivo tak částečně funguje jako plnivo, které pouze pomáhá optimalizovat křivku zrnitosti směsi.
Další důležitou složkou UHPC jsou drátky. Někdy je potom UHPC s drátky nazýváno jako UHPFRC (ultra high performance fibre reinforced concrete).
Tyto drátky mají významně menší rozměr (průměr 0,2–0,3 mm) než drátky běžně používané například do podlah (0,75–1 mm) a jejich množství ve směsi se nejčastěji pohybuje v rozmezí 1–2 % objemově (tzn. 80–160 kg/m3). Drátky nám pomáhají omezit křehké chování betonu a zároveň výrazně zvýšit pevnosti v tahu a využít tak tento kompozit i pro prvky nevyztužené běžnou výztuží.
Konzistence a zpracovatelnost
Konzistence UHPC se může pohybovat v rozmezí téměř zavlhlých směsí až po samozhutnitelné betony. Samozhutnitelná konzistence UHPC je asi nečastější (rozliv obráceným Abramsovým kuželem 650–750 mm, obr. 1), ovšem vysoká stabilita směsi a nutnost dosáhnout co nejvyšší hutnosti betonu vyžaduje často intenzivní vibraci zkušebních těles i konstrukce. Způsob ukládky a intenzita vibrace vždy závisí na konkrétním složení směsi a na její viskozitě. Pokud víme, že konstrukci nebude možno vibrovat, musíme konzistenci směsi přizpůsobit a stejným způsobem jako beton v konstrukci bychom měli ukládat i beton do zkušebních vzorků.
Zejména u směsí vyztužených drátky je vhodné skladbu ověřit rozlivem přes J-ring (obr. 2) a tím ověřit případné blokování drátků. Při zkouškách nesmí docházet k segregaci směsi. Směs musí být dostatečně stabilní pro zvolený způsob ukládky a pro zajištění rovnoměrného rozmístění hrubého kameniva a drátků tak, aby byly zajištěny rovnoměrné mechanické vlastnosti materiálu ve všech místech konstrukce.


Vývoj UHPC v TBG METROSTAV
V TBG Metrostav jsou zkušenosti s vysokopevnostním betonem již od roku 2005 (tzn. s betonem třídy C55/67 a vyšší). Zatím poslední realizací je ukládka vysokopevnostního samozhutnitelného betonu do zárodků oblouku Trojského mostu.
I přesto, že se jednalo o beton třídy C80/95 (90 dní), beton dosahoval v průměru krychelných pevností v tlaku přes 115 MPa, přičemž bylo dosaženo maxima 132 MPa.
K návrhu ultravysokopevnostního betonu ovšem nelze přistupovat jako k pouhému vylepšení betonu vysokopevnostního. K návrhu UHPC je třeba přistupovat jako k návrhu úplně nového materiálu.
Proto byl vývoj zahájen ve spolupráci s univerzitou v německém Kasselu, kde mají s UHPC rozsáhlé zkušenosti. Zároveň byly využity jejich plně vybavené laboratoře pro míchání tohoto typu betonu.
Záměrem výzkumu bylo vyvinout materiál typu UHPC z materiálů dostupných v České republice technologi e v kvalitě minimálně srovnatelné s UHPC používaným ve světě. V laboratořích byly detailně prozkoumány vlastnosti vstupních materiálů, na základě kterých byly sestaveny první receptury. Tyto směsi byly v laboratoři ověřeny a optimalizovány.
V laboratoři na ultravysokopevnostní maltě (bez hrubého kameniva) byla dosažena pevnost v tlaku až 197 MPa na zlomcích trámečků 40x40x160. Po přidání hrubého kameniva byly dosaženy pevnosti v tlaku 192 MPa na krychlích o hraně 100 mm.
Hlavní část vývoje byla a je prováděna na běžných betonárnách TBG Metrostav. UHPC je materiál, který je velmi citlivý na přesný postup výroby, přepravy, na výrobu a zkoušení zkušebních těles i na výrobu finální konstrukce. Bylo proto potřeba tyto postupy přesně nastavit, ověřit a poté udržovat. Zároveň byly odzkoušeny alternativní receptury k recepturám vyvinutým v laboratoři. Bylo totiž zjištěno, že u receptur vyvinutých laboratorně došlo výrobou na klasické betonárně ke znatelnému poklesu pevností i k výrazné změně ve zpracovatelnosti směsi. Směsi vyvinuté v laboratoři tak byly pro naše účely nevhodné.
Muselo dojít k zásadnějším úpravám směsi pro snížení viskozity a zvýšení pevnosti. V rámci těchto zkoušek bylo namícháno téměř 30 různých receptur. Pohled do míchacího jádra při zkušebním míchání UHPC je na obrázku 3.


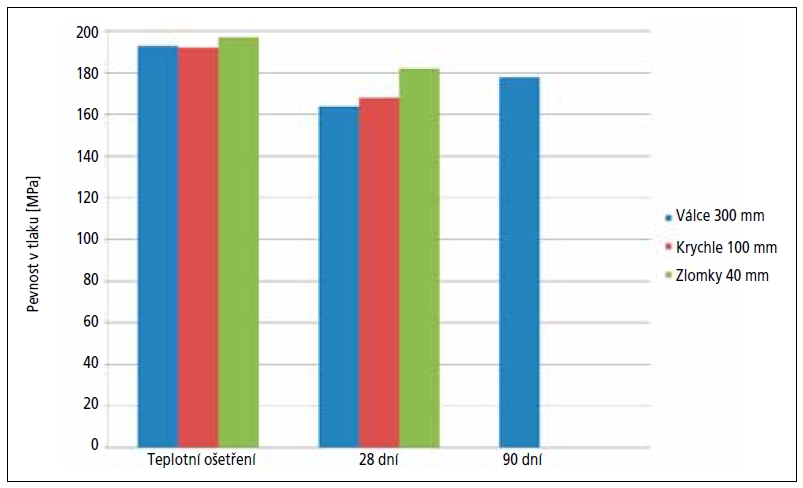


Specifikátor betonu (statik) by tedy měl v projektu specifikovat, s jakou pevností počítá a na jakém tělese má být měřena. Není vhodné trvat na poměru běžně užívaném u standardních betonů. U velkého množství zkoušených receptur byla válcová pevnost srovnatelná s pevností krychelnou.
Pevnost v tahu za ohybu je dalším důležitým parametrem UHPC. Pevnost v tahu za ohybu se nejčastěji zkouší na trámcích délky 700 mm a průřezu 150×150 mm. Pevnost v tahu za ohybu je možno zkoušet pomocí trojbodového ohybu se zářezem (místo vzniku trhliny je pevně dané) nebo pomocí ohybu čtyřbodového (trhlina vznikne v nejslabším místě). Vzhledem k jemnozrnnosti směsi se pevnost v tahu za ohybu dá zkoušet obdobně jako u potěrů, tzn. na trámečcích 40x40x160. Naměřená pevnost je ovšem výrazně vyšší než u předchozích metod. U pevnosti v tahu za ohybu není důležitá pouze její absolutní hodnota, důležitý je i tvar grafu, zejména jeho sestupné části. Pokles by měl být co nejpozvolnější.
Dosažené pevnosti v tahu za ohybu jsou uvedeny v grafu 3. Na statikovi (specifikátorovi) opět závisí předepsání požadovaného typu zkoušky.
Mnohdy důležitější než pevnost je ale reologické chování směsi, zejména její stabilita a viskozita. Bylo tedy potřeba směs zoptimalizovat i z hlediska jejího dalšího využití pro výrobu reálných konstrukčních prvků pro lávku v Čelákovicích. Základem bylo snížit viskozitu směsi při zachování rozlivu a stability směsi. Bylo též potřeba získat zkušenosti s přepravou UHPC autodomíchávači. Vzhledem k tomuto způsobu přepravy bylo též nutno nastavit vhodnou dobu zpracovatelnosti. Doba zpracovatelnosti se v běžných letních podmínkách pohybovala okolo 180 minut. Větším problémem je vysoká lepivost směsi. Kvůli této lepivosti ulpívá relativně velké množství betonu na vnitřním povrchu autodomíchávače a dochází tak ke ztrátám betonu. Zároveň je mnohem problematičtější údržba autodomíchávačů.
Skládání betonu z autodomíchávače do pokusné konstrukce je vidět na obrázku 4.
V rámci zkoušek bylo zabetonováno několik pokusných panelů a prefabrikátů. Optimalizace ukládky a ošetřování probíhala a probíhá se společností Metrostav, divizí 5, v rámci příprav na betonáže prefabrikátů pro konstrukci lávky. Vzhledem ke zvolené samozhutnitelné konzistenci není beton možno ukládat do spádu, na druhou stranu dosahuje požadovaných vlastností i bez vibrace. Důležité je beton ihned po uložení ošetřit, aby nedošlo ke vzniku „oschlé kůže“ (elefant skin) na povrchu konstrukce. Vzhledem k velmi nízkému vodnímu součiniteli beton osychá velmi rychle (během několika minut). „Oschlá kůže“ jednak nedosahuje požadovaných pevností, ale hlavně zadržuje unikající vzduch z betonu a povrchová vrstva pak není soudržná se zbytkem konstrukce. Ukládka a zatékání betonu do konstrukce je vidět na obrázcích 5 a 6.


Závěr
Je otázkou, zda se dá UHPC ještě považovat za beton, nebo zda už jde o speciální kompozit na bázi cementového pojiva. V každém případě jde o velice zajímavý materiál blízké budoucnosti, který nám umožní budovat subtilní lehké konstrukce s výrazně prodlouženou trvanlivostí. Kromě samostatných konstrukcí je možné s tímto typem materiálu vytvářet ochranné tenké vrstvy na standardních konstrukcích, např. přímo pojížděné ochranné nabetonávky mostovek, ochranné vrstvy mostních říms nebo pilířů. Ve světě už se UHPC pro tyto účely začíná využívat.
V TBG Metrostav je technologie výroby a přepravy UHPC zvládnuta a je možné UHPC, tzn. beton s válcovou pevností vyšší než 150 MPa zákazníkům dodat. Na beton třídy C110/130 už byl vydán i certifikát, vyšší třídy je možno certifikovat dle potřeby zákazníků. Více informací o UHPC firmy TBG Metrostav najdete zde.
Pozn.: V článku jsou uvedeny některé výsledky z projektu MPO ČR č. FR – TI3/531.
ROBERT COUFAL, JAN L. VÍTEK
foto archiv firmy TBG METROSTAV, s. r. o.
Ing. Robert Coufal, Ph.D., (*1980)
absolvoval České vysoké učení technické v Praze, Fakultu stavební. Pracuje jako technolog ve firmě TBG METROSTAV, s. r. o., kde má na starosti výzkum a vývoj nových produktů.
Prof. Ing. Jan L. Vítek, CSc., (*1957)
je autorizovaným inženýrem pro obor mosty a inženýrské konstrukce. Pracuje ve funkci experta v a. s. Metrostav a přednáší na Stavební fakultě ČVUT. Je místopředsedou České betonářské společnosti ČSSI. V Mezinárodní organizaci pro konstrukční beton (FIB) vede pracovní skupinu zabývající se mezními stavy použitelnosti.